The saree was the attire most preferred by women in those days. I, too, wore sarees at home and for evening outings. My go-to style was a nice, crisp cotton or organza saree with a pearl string or some other traditional jewellery. Chiffon sarees were very glamorous too, and the silks were reserved for winters, to be worn with nice colourful shawls. I did have a few leggings, with straps below the foot, which I used to wear with loose men’s shirts. It felt very trendy and experimental as very few women wore this.
I noticed that there was a lacuna in women’s daily wear wardrobes and the salwar kameez, worn mainly by women in Punjab, could fill that gap. I thought I could design printed cotton suits for women and sell them from home. But for that, I needed capital to start my business, as I did not have any money and we didn’t have any savings either. I did not even have a bank account.
I discussed this idea with Satish, who looked very sceptical and was non-committal about my new venture, almost dismissing it in his mind as a waste of time and as one of my fanciful ideas. I was, therefore, very surprised when a couple of weeks later he informed me that my loan of Rs 8,000, which he had applied for, had been sanctioned by Syndicate Bank and I could use this money for my business if I wanted to (I did wonder why he didn’t ask for Rs 10,000). I was quite thrilled that at least he took the trouble to apply for a loan and succeeded in getting it. However, Satish cautioned me that the loan had to be paid back to the bank with interest and that I should be very careful with the money, as I would have to pay it back. Then he left me with “unasked for” husbandly advice: “Now you will finally realise how difficult it is to earn money.” I desperately wanted to prove him wrong.
Once I had some capital, I began wondering where to start. Finally, armed with Rs 4,000 (I did not want to risk the entire sum), I set out for the market one day. I did not know much about the Bombay of those days, as it was almost a new city to me; I had lived there 15 years ago for a very short period. So, I decided to take the plunge. I got into a taxi and asked the driver to take me to a fabric wholesale market. The driver dropped me in front of a wholesale market somewhere near Bhuleshwar (I discovered later that there were many such markets in Bombay). I can still recall the sheer delight I felt at seeing rows and rows of fabric shops; I was not sure where to start. I didn’t have much of an idea about buying fabric from a wholesale market. There was so much choice, but I kept it simple and came back home with some greige cotton fabric and some mulmul (voile). On reaching home, the tough task ahead sank in. I only knew a few naval friends, and the probability of them knowing any tailor or block printer was rather low. It did seem like a big challenge and I was wondering whom to ask for help. I had to find a block printer and a tailor to kick-start my small venture. At last, as luck would have it, I got my first big break.
My old naval friend Bala Agarwal heard about my plans and predicament, and stepped in to help me. She introduced me to Devesh Sadh, a block printer who had a large printing factory and who, as I would soon discover, proved to be a big help. His family had been in this business for many years and I was the beneficiary of all this experience and knowledge, which he shared so generously with me. At times, he would get his old workers at the factory to demonstrate to us some old techniques of block printing. Meeting Devesh was a very important step in my journey, as he made my work easy, smooth and fun; he helped me to immediately kick-start my production of printed suits.
Bala knew Devesh very well. His family used to print sarees and had a large modern factory. Devesh himself was a young, enthusiastic and educated entrepreneur who was keen to contribute and learn. We made a very good team because we were both learning on the job. He was always very eager to experiment with different ways of using blocks. His factory was like a treasure trove of old and beautiful wooden blocks.
The thrill of creating new designs using colours and blocks was unparalleled. The wooden trolley with the ready colours to be used for printing was in itself a beautiful piece of equipment and looked attractive. The trolley used for printing was old and beautifully designed. It was also found to be very practical, as it was on wheels and easy to move around the table on which the 6-m fabric was stretched up for printing. Old traditional items always had great beauty with practicality. Together, we experimented with different blocks of butas (motifs), jaals (lattice) and borders, and tested different colour combinations. We would first print the design on an old newspaper to see how it looked and then do the final printing on fabric. For someone who had never stepped inside a block print factory, the experience was very new and exciting for me. The designs were coming out instantly as we went along with the prints and new colour combinations. The block print factory had a very creative air, which was full of possibilities. One had to pick up the right block and the right colour schemes, and give shape to one’s ideas. If I visit a block print factory even today, I would find it truly creative though very basic, as it is a very old method for printing and the tools have not changed much over the years.
Block printing is a process of printing patterns by means of engraved wooden blocks. It is done by hand and is therefore a slow process. It is, however, capable of yielding highly artistic results, some of which are unattainable by any other method. The method of block printing in India goes back to the Indus Valley civilisation. The tiny imperfections and variations caused by the human hand create the main beauty of the prints, which are very unique, and no two pieces printed will be exactly the same. This lends uniqueness and beauty to the garment. I was known for beautiful block-printed cotton suits and they became my hallmark. Biba has always remained strong with its print language.
Rajasthan is known for its block printing industry and traditional process of block printing on textiles with rich colours. The tradition of block printing has been practised in Rajasthan for more than 500 years. It was introduced by the Chhipa community (located in the village of Bagru in Rajasthan). They introduced the intricate floral motifs that became very popular and are still used in a lot of sarees, suits and even household furnishings. The beauty is that they lend themselves to traditional and contemporary clothing seamlessly.
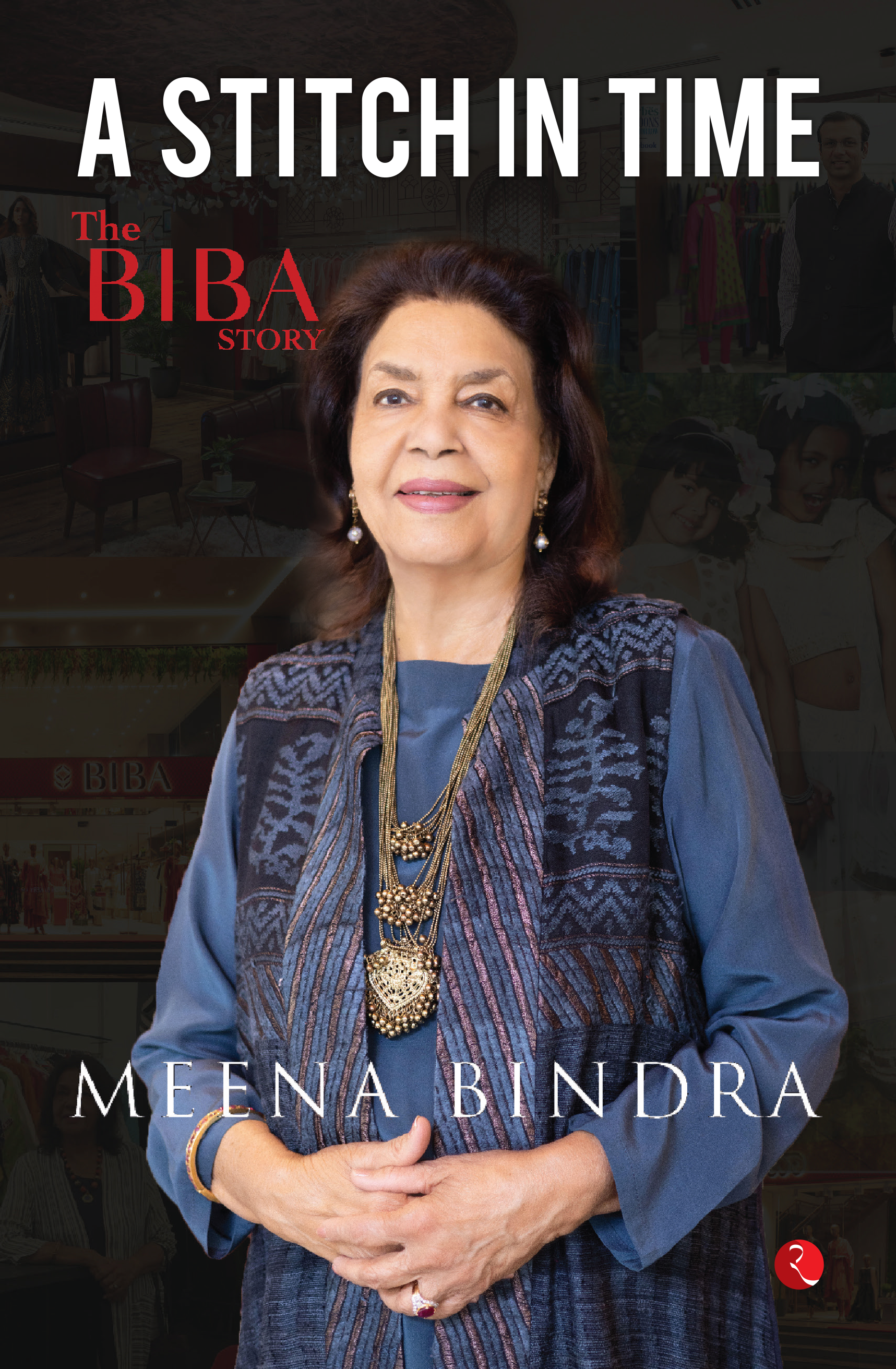
Excerpted with permission from A Stitch in Time: The BIBA Story, Meena Bindra, Rupa Publications.