The main drive to zero in the chemicals industry currently revolves around zero carbon emissions. This is a major challenge for an industry that is highly energy-intensive, particularly sectors like cement, steel and glass production that require high temperatures and substantial energy consumption. These sectors are now intensely focused on reducing their carbon emissions to zero.
Key strategies have been brought into play to reach the industry’s net-zero target by 2050: operational decarbonisation, carbon capture and storage (CCS) technologies, and renewable and sustainable feedstocks. The electrification of plants and incorporating green hydrogen directly into industrial processes, such as using it in blast furnaces or relying on biomass as a carbon source to reduce metal ore usage, are just some of the approaches being adopted. Beyond that, the broader chemical industry is working on producing zero-carbon products, ranging from resins and polymers to coatings.
A disruptive innovation that aligns with this zero-emissions ambition is the push to use zero crude-oil feedstock. In this regard, hydrogen steps up as a game changer, not only for its potential in clean energy but also in producing eFuels and eChemicals.
As the name suggests, rather than being manufactured through traditional refining, eFuels are electrically produced and are touted to be the fuels of the future. These liquid fuels are not linked to batteries but can serve as direct drop-in replacements for gasoline and diesel. While they are chemically very similar to their fossil-fuel counterparts, eFuels are dissimilar in that they are derived from water and carbon dioxide (or biomass) using electricity. They have the added benefit of being much lower in sulphur and other contaminants, making them cleaner alternatives.
eFuels are created by splitting water into hydrogen and oxygen using electrolysis—an energy-intensive process that, when powered by renewable sources like solar or wind power, is incredibly clean. The green hydrogen produced is then combined with captured carbon dioxide or carbon monoxide in a Fischer-Tropsch reaction to create e-gasoline, e-diesel, e-jet fuel and other e-heating fuels. What makes this even more environmentally friendly is that the carbon dioxide used can either be captured from industrial emissions or pulled directly from the atmosphere, further reducing the overall carbon footprint.
There are other emerging technologies for producing e-Fuels, such as direct electrolysis of carbon dioxide, microbial electrosynthesis, photoelectric synthesis and plasma-based conversion. But the Fischer-Tropsch process is by far the most industrialised and widely adopted.
Another innovation on the road to zero crude-oil dependency is biorefining, which merges the concepts of zero carbon and zero oil feedstocks. Biorefining involves producing chemicals in bioreactors through processes like fermentation or pyrolysis. Chemicals such as succinic acid, lactic acid, glycols, ethylene, ethanol and methane can be derived from biomass, with the ultimate goal being the use of household waste as feedstock.
While there has been considerable interest and investment in biorefining, and companies like BioAmber have successfully produced bio-based chemicals as drop-in replacements for crude oil chemicals such as succinic acid, the sector has faced challenges. Competing with the cost-efficiency of oil-based alternatives is difficult, particularly when oil prices drop, often undermining these nascent ventures. However, with the rising focus on zero carbon and sustainability, companies involved in biorefining are gaining new momentum.
Zero accidents and zero plant downtime
Moving beyond emissions, achieving zero accidents and zero plant downtime remains a top priority for the chemical industry. This has always been a fundamental goal, especially given the catastrophic consequences of industrial failures such as the Bhopal gas tragedy in India in 1984, where a pesticide plant leak resulted in thousands of deaths. But more recently too, plant accidents and shutdowns have plagued the chemical supply chain, reminding us of the need for constant vigilance. A fire at BASF’s Ludwigshafen plant in 2017 caused a shutdown and force majeure on some of its products, affecting many downstream markets. Another fire – this time at Huntsman’s MDI site in August 2024 – was similarly attributed to force majeure. Digital monitoring, sensors and predictive maintenance, powered by AI and other advanced tools, are becoming essential to prevent accidents and minimise downtime. These technologies offer real-time insight into plant conditions, enabling early detection of potential problems and making the goal of zero accidents and zero downtime more attainable.
Zero reliance on overseas suppliers
Another key objective for many companies in the chemicals industry is zero reliance on specific geopolitical regions, particularly China. The COVID-19 pandemic underscored the vulnerability of global supply chains, bringing into particularly sharp focus how dependent many businesses had become on Chinese supply chains. As a result, companies are now looking to reshore some of their operations, or at least diversify their supplier base, to reduce risks. Technologies like 3D printing and industrial automation are playing a big role here. With 3D printing and industrial automation, companies require less labour (which translates to lower associated costs) and can produce plastic and metal parts locally. This technology allows for greater flexibility, faster production, and ultimately, reduced dependence on low-cost overseas suppliers.
Beyond zero carbon
While zero carbon is the immediate goal, it’s only part of the picture. The next frontier could involve tackling other harmful emissions. Zero NOx and SOx emissions – nitrogen and sulphur oxides that contribute to air pollution – are becoming key targets, especially as governments clamp down on vehicle exhaust fumes.
Then there’s the issue of zero heavy metals. Heavy metals like mercury and chromium can bioaccumulate, especially in marine ecosystems, leading to contamination of fish stocks. In the digital and electrical age, where metals are more heavily used in technologies like electric vehicle motors and batteries, managing heavy metal disposal and manufacturing waste will become increasingly important. The industry is already addressing chromium removal in cement production, but we’re likely to see more focus on heavy metals in the years to come. Accordingly, disposal and manufacturing waste will need to be addressed and monitored.
Zero water pollution
Zero water pollution is also climbing the agenda, particularly as the demand for clean, fresh water intensifies. Technologies like Zero Water Discharge (ZWD) systems, which can treat and reuse wastewater on-site, are becoming more appealing. Although current regulations don’t require widespread adoption of these systems, public pressure is growing. We’re seeing increased awareness of the state of our rivers and lakes, driven by high-profile events like the 2024 Paris Olympics, where the poor water quality of the River Seine had to be addressed before triathletes were ready to take the plunge.
This rising concern is likely to spur governments and water companies into action, and we can expect a push for technologies that address water pollution, such as active pollutant removal systems for chemicals like PFAS from ground and water sources. With these developments, opportunities for ZWD systems, water centrifuges and spiral membranes are set to grow.
Conclusion
The chemicals industry is on an ambitious path to zero with zero carbon emissions, zero accidents, zero crude-oil reliance, zero plant downtime, and zero environmental impact. From eFuels and biorefining to advanced digital monitoring and sustainable supply chains, from tackling other harmful emissions to working on eliminating water pollution, the pursuit of a sustainable chemical industry is well underway
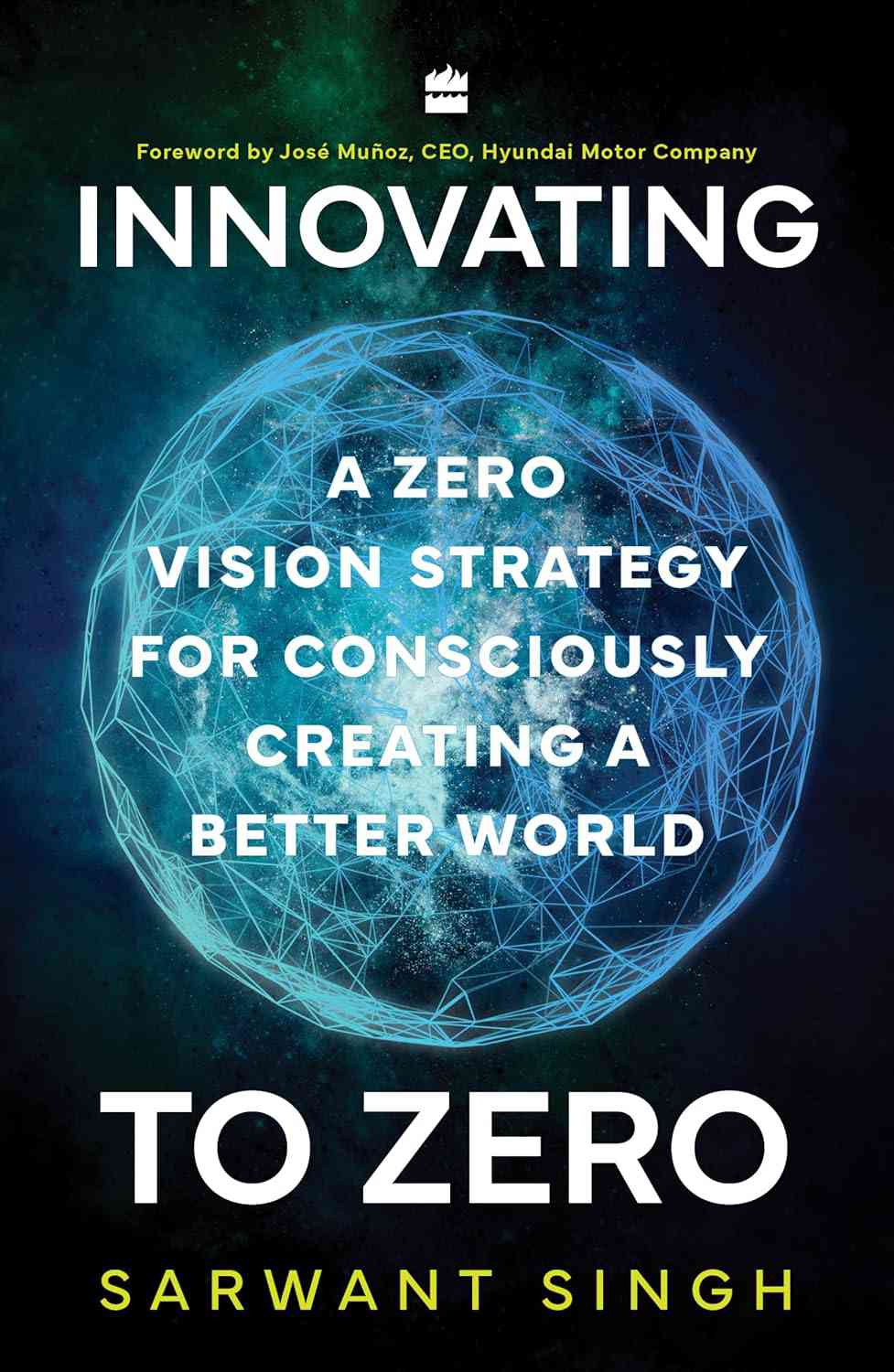
Excerpted with permission from Innovating to Zero: A Zero Vision Strategy for Consciously Creating a Better World, Sarwant Singh, HarperCollins India.