India’s tour of South Africa has been played in two distinct parts: one which saw the hosts win the first two Test matches and the series, and the other in which India have so dominated that South Africa’s win in the rain-curtailed fourth ODI seemed like nothing more than an aberration.
As Kohli and Co cruised to victory in the fifth ODI, there was a familiar sense of inevitability; a sense that has been built upon an unshakeable self-belief. Two stinging defeats in the first Two tests would have broken the morale of lesser sides but India found a way to turn it around to clinch the first ever bilateral series win in SA.
Yes, the formats are different but it is still South Africa.
Yes, this South African side looks a little green behind the ears but you still need to beat them.
Yes, the pitches have been almost “Indian” but you sill need to make it count.
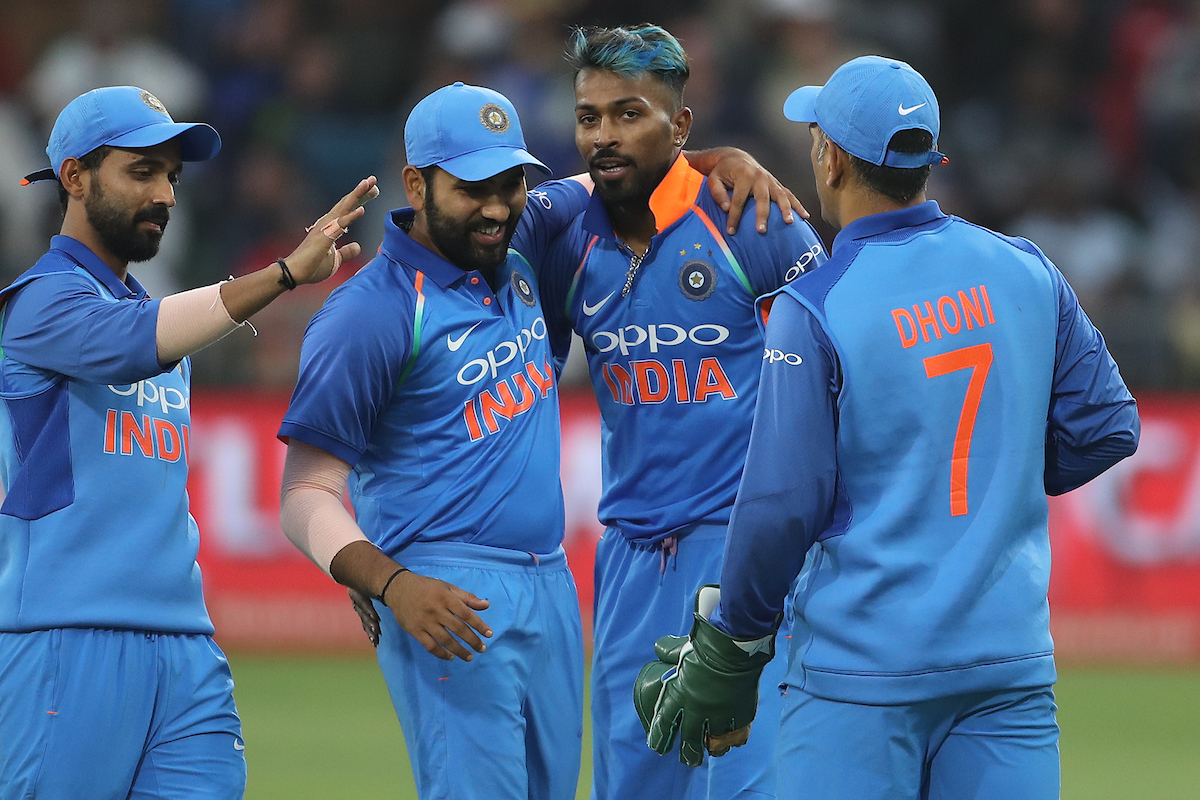
None of it would have mattered if India were not prepared to take advantage of things going their way. If there is anything this Kohli side does by default, then going for the jugular will rank high in that list.
Never too late
Just ahead of the third Test at the Wanderers, the India skipper had spoken about how it’s a never a bad time to start winning. Many teams might have wanted to just get things over with (given that the series was lost) but not this Indian squad. Ravi Shastri and Kohli chose to look at the positives and the opportunities that presented themselves. They wiped the slate clean and began again.
“Well, look, we have looked at the positives from the first two games as well, not many times on overseas tours we have picked 40 wickets in two Test matches. So, I think that’s a big boost for us. If the bowlers can continue doing their job, and as I said before the series that whichever side bats better wins the series, and that’s been the case so far,” Virat had then said.
“But it’s never a bad time to start anything, that’s what I believe in and, as I said, batsmen are looking to rectify their mistakes that happened in the first two games. Because it’s a chance for everyone to step up in times that have not gone our way and to change things around for us. That will build characters, that will build individuals and that will build personalities. That can be a milestone for guys going to forward if they can step up in this game and be the difference for us in this Test match. So it’s never a bad time to start,” he had further added.
This was also Kohli trying to desperately drum up some resistance and the team responded. They started up. And they won a Test match played in extremely trying conditions. The momentum shifted India’s way and now, there is no stopping them.
All that positivity that Kohli kept trying to drill into the team finally made its way through; it finally made believers of them all and perhaps us too.
Positive psychology puts all the focus on the individual and asks whether or not we are ready to take ownership of our own lives and stop seeing ourselves as powerless victims – It is a notion that can be traced back to Martin Seligman’s research in the 1960s.
This is exactly what Kohli and Shastri have been demanding from this unit. The impact of these words will naturally vary from player to player but as long as they all start moving in the same direction, things will only get better.
Shikhar Dhawan (305 runs @ 76.25) got among the runs in the ODIs, Kohli (429 @ 143.00) seemed unstoppable as always, the wrist spinners – Yuzvendra Chahal (14 wickets @ 16.00) and Kuldeep Yadav (16 wickets @ 11.56) – broke records and everyone chipped with enough runs or wickets to keep the wins coming. The early losses hurt but the response to them is heartening at many levels. Indeed, now we are once again wondering what wonders some proper preparation might have achieved.
After winning the series in the fifth ODI, Kohli once again brought up the win in the third Test — it is clear to him that the performance India put up in that Test will have an impact way beyond the South Africa tour.
Most wins after first 48 ODIs as captain
— Mohandas Menon (@mohanstatsman) February 14, 2018
37 - Clive Lloyd
37 - Hansie Cronje
37 - Ricky Ponting
37 - VIRAT KOHLI#SAvInd
-------------
Most wins after first 35 Tests as captain
27 - Ricky Ponting
25 - Steve Waugh
21 - Michael Vaughan
21 - VIRAT KOHLI
“Every since the third Test in Johannesburg it’s been a wonderful time for us. We have really enjoyed ourselves and played some wonderful cricket. So the boys can be really proud of the effort they have put it. It has been a collective effort of the boys and the management to be able to create history,” he said in the post-match presentation.
Failures have their own lessons to teach and so do victories but the great teams find a way to get better regardless of the result. Under Kohli, in South Africa, this team has done exactly that and in the long run, that’s all that matters.