Over the last decade, the waste industry has been quietly growing.
Given the growing rates of trash generation, this is hardly a surprise. In 2012, the world generated 1.3 billion tonnes of municipal solid waste per year. According to a 2018 World Bank report, this number is set to hit 3.4 billion tonnes by 2050. To meet this demand, the global waste management market – which was estimated at $400 billion-$1,600 billion in 2020-2021 – is expected to reach $700-$2,483 billion by 2030.
India, with its growing population and rapid development, has a waste management industry estimated at $1.3 billion (Rs 9,656 crore). As of January 2020, estimates indicated that the country handled approximately 0.15 million (1,50,000) tonnes of solid waste. Of the 54 million tonnes of solid waste produced in this year (2019), 3.3 million tonnes was plastic.
As per the Central Pollution Control Board plastic waste management guidelines, all plastic waste must be segregated with non-recyclable plastics to be used in road laying, waste-to-energy projects, or conversion into refuse-derived fuels; and only a small fraction of non-recyclables should be disposed of in sanitary landfills.
However, this rarely occurs. In 2019-2020, only 60% of India’s plastic waste was handled according to the Central Pollution Control Board’s guidelines. The remaining was likely burnt, lost in nearby water bodies, or dumped as mixed waste into landfills, which are usually nothing more than vast, poorly maintained, overflowing dumpsites.
Open dumping
In India, landfills – synonymous with open dumping in many countries around the world – are undoubtedly the cheapest, short-term option for managing solid waste, which usually contains about 6% plastic. Today, only 20% of collected waste is sorted and processed, while 80% is dumped as mixed waste into the 1,684 landfills that India currently has. On average, most urban local bodies spend Rs 500- Rs 1,500 per ton of waste in “tipping fees” for collecting, transporting, treating, and disposing of waste in dumpsites.
A 2021 study from the Indian Institutes of Technology-Bombay, which assessed different waste management scenarios for the 9,000 tonnes of solid waste produced daily by Mumbai, confirms that landfills are the most monetarily economical option. It compared the capital, operations, and maintenance costs of running a material recovery facility (to sort waste into recyclables and non-recyclables) with incineration, composting, or landfills.
Costs were offset by income from compost and electricity through waste incineration and biogas. The results showed that recovering recyclables and using landfills are the least expensive way to handle waste over 20 years. This system is likely to cost $19 (Rs 1,400) per tonne, whereas incineration would cost nearly double, $36-$38 (Rs 2,800 per ton).
Yet, landfills are not sustainable as mixed waste has severe ecological effects due to substantial emission of greenhouse gas such as methane and production of leachates. Leachate is a form of “liquid pollution” containing many toxins and pathogens that is formed when water seeps through waste piles.
Currently, most landfills in India are overfilled and new landfills are difficult to establish in the face of stiff local resistance and skyrocketing prices of urban/semi-urban land. The poor condition of Kanjurmarg, Mumbai’s newest waste management site with a material recovery facility and bioreactor landfill, exemplifies the failure of the system.
The costs of dumping mixed waste have been building up over several decades, ranging from large-scale fires due to methane generated by biodegradable waste to leachates poisoning local water sources. Toxic chemicals and microplastics leaching out of untreated waste piles are lowering life expectancies of locals.
Calculations show that Delhi’s three landfills at Okhla, Bhalswa and Ghazipur are collectively responsible for environmental damage worth Rs 450 crore as per a 2018 study by the National Environmental Engineering Research Institute, Central Pollution Control Board and the Indian Institute of Technology-Delhi.
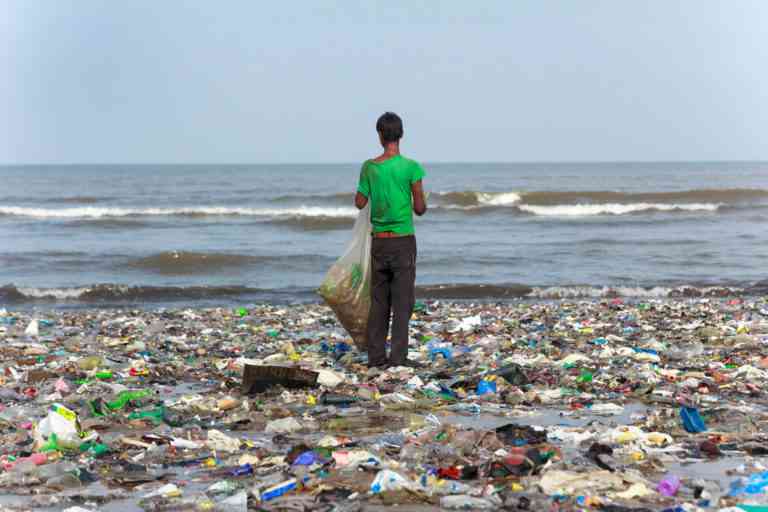
Waste segregation does not stop the majority of plastic waste from entering landfills or being dumped, as only high-value plastics like polyethylene terephthalate and high-density polythethylene are recovered for recycling.
The vast majority of single-use plastics, multilayer packaging and polystyrene end up in open dumps, eventually leaking into the environment. A 2020 report from the National Productivity Council in partnership with the CounterMEASURE project outlines how open dumping of mixed waste in cities leads to plastics entering rivers and seas.
The latest UN Environment Programme report on marine plastics estimates that land-based sources contribute 80% to the 11 million tonnes of plastic entering the oceans annually. The report also highlights the huge impacts of marine plastic pollution on wildlife, human health and climate change; these negative impacts likely cost the world $3,300–$33,000 per tonne per year in terms of reduced natural capital in affected ecosystems.
Since the cost of open dumping/landfilling plastic waste is extremely steep in the long run, especially for environmental health, is it perhaps better to burn plastic waste for energy?
Cost of burning
Incineration has been a strategy for handling plastic waste in many countries. Japan and Singapore have been incinerating 37% and 78% of their municipal solid waste since 2017 and 2015, respectively. The waste-to-energy incineration market in China has vastly expanded since 2017 and the country plans to build a further 600 plants by 2025. Sweden began importing trash from other European countries in 2016 to power its waste-to-energy plants. However, waste-to-energy in India has had a stormy past and will likely have a rocky future.
In 1987, the first waste-to-energy plant in India was constructed at Timarpur, Delhi, to generate 3.75 megawatts of electricity by incinerating 300 tonnes of waste per day. As the plant received low-calorie waste (600 kcal-700 kcal/Kg) instead of high-calorie waste (>1,462 kcal/Kg) it was shut down 21 days after it began operations. Since then, India has installed 14 more waste-to-energy plants of 130 megawatts capacity, of which half have been shut down while the operational ones are under scrutiny for environmental safety violations. In February 2017, the National Green Tribunal fined the Okhla waste-to-energy plant Rs 25 lakhs for violating environmental safety norms.
Waste-to-energy plants have been unsuccessful in India due to several reasons. Firstly, most waste-to-energy projects rely on fuel from municipal solid waste, which in India, is of low calorific value. Secondly, waste-to-energy plants are expensive; despite several financial subsidies and incentives, electricity produced by these plants costs more (Rs 7/kWh) than electricity from coal/solar plants (Rs 3-4 /kWh). Lastly, these plants often burn mixed waste unsuited for incineration and manage emissions and fly ash so poorly that they are extremely polluting.
Yet in 2017, the National Thermal Power Corporation invited developers and investors to set up 100 waste-to-energy plants in the country. The Ministry of New and Renewable Energy aims to generate 0.5 gigawatts of energy from waste-to-energy projects across India and has reached 40% of its goal.
“Although past waste-to-energy projects were unsuccessful, the technology can still be useful,” said Swati Sambyal, an independent waste and circular economy expert. “Waste composition in cities is changing. Plastic waste fractions are rising, but most cities do not inventory waste. Without this data, the usefulness of waste-to-energy is moot.”
Sambyal points out that data-backed decisions must drive the technologies used for handling waste, and not the other way around. “But right now, many waste-to-energy plants are being set up without a thorough understanding of the waste that will power the plant,” she added.
Apart from waste-to-energy plants, coprocessing – using plastic waste as an alternative fuel – in cement kilns is another way to burn plastic gainfully. Typically, cement plants obtain segregated municipal dry waste and extract combustible material to make refuse-derived fuel.
“However, coprocessing has been marred by many cost issues,” said Kaushik Chandrasekhar, a solid waste management expert from The Energy and Resources Institute. “Typically, the quality and quantity of municipal waste is not optimal for refuse-derived fuel. So, cement plants need to spend money on pre-processing waste to make it useful.”
“Then there is the transportation cost – who pays for transporting waste from cities to the cement plants? This cost is huge as the waste has to be transported hundreds of kilometres to cement plants,” he added.
Therefore, if burying plastic waste and burning are both expensive, recycling plastic may prove to be a better solution than either. A 2005 US case study seems to support this by showing that recycling consumes lesser energy and creates fewer environmental burdens than either landfills or incineration.
Cost of recycling
“Frankly, we do not really know, especially for India,” said Sambyal. “Also, most plastic is never recycled in the true sense of the word. It is all downcycled, meaning that the plastic is downgraded to a lower quality.”
In addition, data on plastic recycling in India is woefully incomplete. In the Central Pollution Control Board’s 2019-2020 annual report on plastic waste management, only 14 states have detailed data on plastic waste usage and recycling and most reported numbers of recycling units are clubbed together with manufacturing units.
The greater part of recycling in India occurs as “backyard recycling” where waste pickers sort plastic waste by hand, wash it in drums, and pass it through single-unit extruders that mechanically shred and melt it to form granules and pellets. According to the PlastIndia Foundation, the plastic recycling industry in India employs over 1,00,000 people with a majority (10,000+ units) in the unorganised sector as compared to the organised sector (100+ units).
“Most of our recycling is through the informal sector which has invested its own money and runs small plants,” said Bharati Chaturvedi of Chintan, a Delhi-based environmental research and action group. “These plants can be polluting, but there have been no efforts to help them find better solutions.”
“Despite its issues, this sector is still helping to curb plastic pollution, and a lot can be achieved by formalising and upgrading this sector in scale, capacity and technology,” she added.
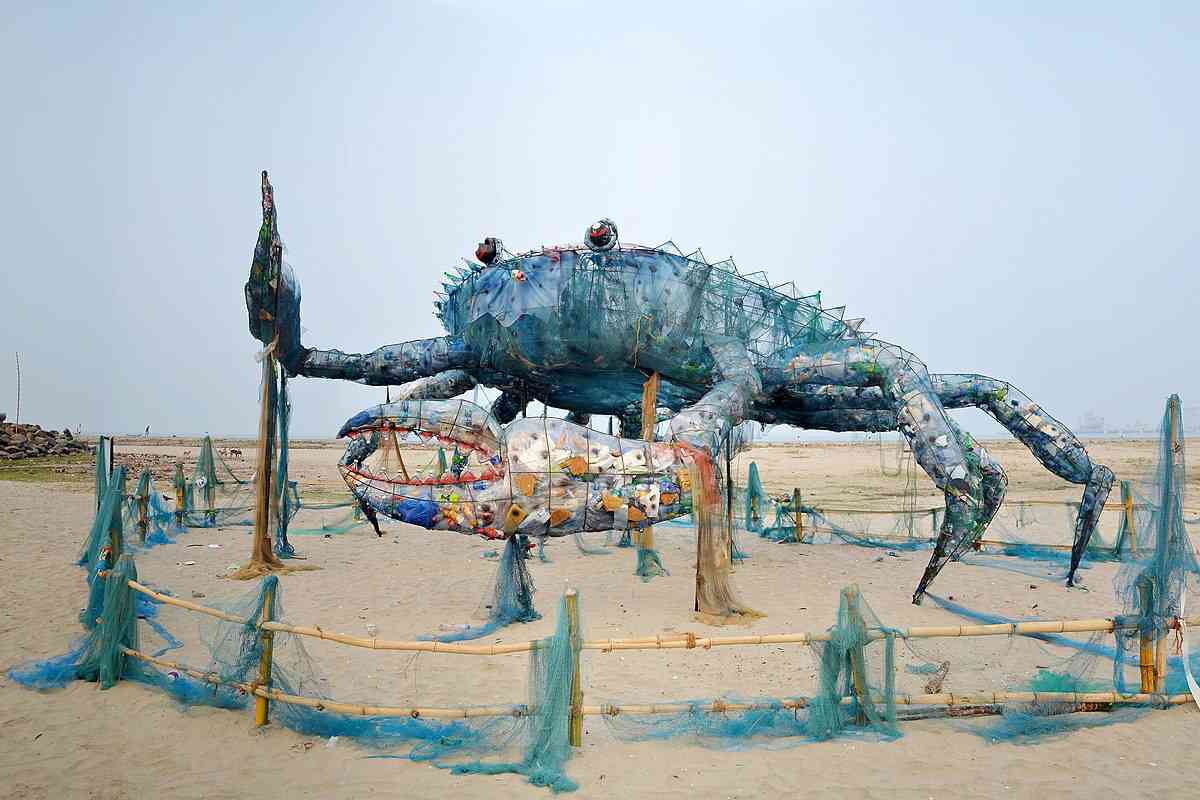
Sambyal said, “Crude recycling by the informal sector not only releases hazardous emissions but also causes a lot of plastic leakages.”
“Since the sector is informal, most plants cannot afford to clean dirty plastic,” she said. “So, material contaminated with wet waste is dumped into drains or at roadsides. There is not enough evidence to establish how polluting recycling is, which is why the true cost and ‘environmental friendliness’ of recycling is unknown.”
Issues with downcycling and estimating the true costs of plastic recycling are global problems. This is because currently, scaling-up chemical recycling methods which minimise downcycling, are financially unviable and the true cost of recycling plastics is often unknown due to the sheer variety of plastics produced. Usually, no information on either the plastic’s characteristics or the additives used to create it are available to recyclers, which makes it hard to predict if plastic waste is safe or even suitable for recycling.
Despite these setbacks, recycling still has enormous potential to reduce the industrial and environmental costs associated with the production of virgin plastic from fossil fuels. Recycling one tonne of plastic is estimated to save 13.8 barrels of oil, 5,744 kWh of energy and 810 cubic feet of landfill space.
But until the day that a plastic bottle or polythene bag is converted back into a plastic bottle or polythene bag, respectively, recycling will remain short of what it promised.
This article first appeared on Mongabay.