If you’ve ever had to deal with a punctured tyre while on the road, you know how this annoying setback can cause delays in the schedule you had planned for the day, leaving you with the feeling that you’ve “lost” the race against time.
Imagine yourself in a car race, where a punctured tyre seems like the thing that could put you out of the race entirely.
Not so if it’s a Formula One race.
During the 2008 Monaco Grand Prix when Lewis Hamilton hit a barrier in heavy rain, it left him with a punctured tyre and the commentators lamenting Monaco’s notoriously difficult circuit with great animation, as Hamilton was forced to make a pit stop. In contrast, if you were to instead listen to team McLaren’s internal feed while the same incident was happening, you would hear information and a few short instructions being calmly communicated between the team and Hamilton, and then silence until Hamilton emerges from the pit stop nine seconds later.
While an average pit stop in a race takes two to three seconds, even in this less-than-favourable situation, it took the team less than ten seconds to make the switch to a different tactic, which, besides changing tyres, involved making alterations to car components and fuelling up. Hamilton went on to win the race that day, and the drivers’ championship as well.
It is from incidents like this on the Formula One track that McLaren’s Geoff McGrath was able to draw a parallel with improving the efficiency of a production line at GlaxoSmithKline (GSK) back in 2011.
If you’re wondering what someone from a racing car company was doing at a pharmaceutical company, McGrath used to head McLaren Applied Technologies (MAT; now Mclaren Applied Limited), a spinoff of McLaren that applies Formula One’s high-performance culture and working methods to other businesses. When team MAT collaborated with GSK in 2011 to figure out how they could reduce production cycle time at GSK’s toothpaste factory in Maidenhead, England, they discovered that ‘a production-line bottleneck was occurring during the so-called changeover: “transition periods when factory workers needed to switch products on the line from one toothpaste brand to another. This meant changing and cleaning the tubes, rearranging the tools in the line and a number of other procedures that halted production.”
For McGrath, the parallel with a Formula One pit stop was obvious: “If we can change four tyres on a Formula One car in two seconds, why does it take us two hours to do a changeover in the toothpaste factory?”
The GSK and McLaren teams worked together to apply processes and procedures used at Formula One races to the factory’s production line. They asked questions such as whether the tooling was standardised and if the changeover team was specially picked or was just made up of whoever happened to be available at the time the switchover to a different toothpaste cycle was being made; they made a computer model of the production line – similar to what is done for Formula One races; they even put the shop floor workers in McLaren overalls and instead of telling them what to do, let them play around with the system to figure out what needed to change.
The result was that by drawing a parallel with how the McLaren Formula One team develops a predetermined plan for any possible scenario during a race (the reason they immediately knew what to do when Hamilton had the punctured tyre), the team at the toothpaste factory “developed a seven-step process that began before the changeover, mirroring McLaren’s cycle of simulation, pre planning, debriefing and continuous improvement. Changeover times fell by 60 per cent, dropping from an average of 39 minutes to 15, equating to an extra 20 million tubes by the end of the year.”
The pit stop analogy also led to a change in perception. As Shaun Glover, engineer at GlaxoSmithKline, put it, “We used to see changeovers as down time; McLaren sees pit stops as an opportunity to win the race.”
While increased productivity is one positive impact of using Formula One-developed processes to improve cycle times, there are several other related positive outcomes that a company can benefit from, some of which are:
• Being able to produce more in a given time period could result in less raw material inventory and fewer man hours (lower labour costs), which directly impacts profit margins.
• Improved customer satisfaction could result from having a shorter time to market. In the services sector especially, a rapid turnaround time is vital to improving customer responsiveness, satisfaction and delight.
• Being able to rapidly churn out products, especially high-technology ones, gives companies a competitive advantage in terms of the ability to provide innovative solutions and meet launch dates sooner. An inability to do so runs the risk of rendering cutting edge R&D departments obsolete, if production cycles are not able to keep pace.
• The cost savings gained by a higher product output and a leaner manufacturing cycle also provides opportunities to experiment with new products. Companies with lower cycle times can turn their attention to developing prototypes or samples for consumers, allowing them to develop new and innovative products.
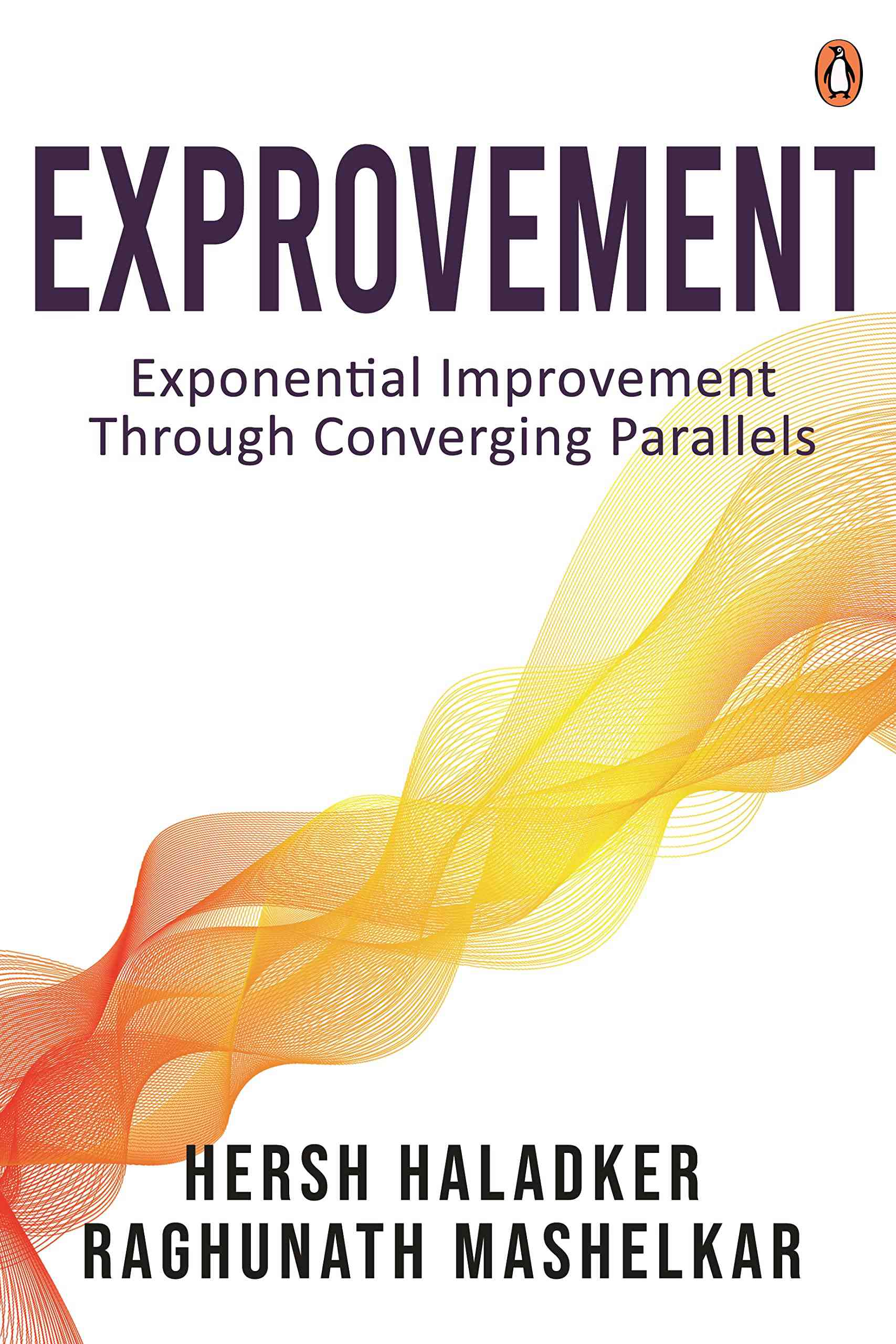
Excerpted with permission from Exprovement: Exponential Improvement Through Converging Parallels, Hersh Haladker and Raghunath Mashelkar, Penguin India.