For most of the 20th century, manufacturing three-dimensional solid objects usually took two forms. Some processes involved shaping material inside a mold, such as injecting molten plastic into a tooling, or shaping heated metal in a press. Other processes involved selectively removing material from a block or sheet, much like a sculptor chipping away at a marble block to carve a statue. Both of these methods have major disadvantages. Creating moulds is very expensive, and the moulds are quite hard to modify once completed. By comparison, so-called subtractive manufacturing wastes a lot of material and is unable to produce certain shapes.
In the 1980s, though, a new family of technologies began to emerge. Unlike previous methods, they created parts by stacking or depositing relatively flat layers and building them up into a three-dimensional shape. These techniques have come to be known as additive manufacturing, three-dimensional printing, or 3D printing.
The most common types of 3D printers work somewhat like an ink-jet printer. A typical ink-jet passes back and forth over a piece of paper, squirting ink from a cartridge out of a nozzle in the places software directs it to. Instead of ink, 3D printers use a material like plastic and heat it until it is soft. Their nozzles deposit the material, following a software-run pattern for each layer, repeating the process many times as the object gradually becomes more three-dimensional. The layers fuse together as they harden, and the finished object is ready to use. Over the past two decades, 3D printing has continued to advance in terms of higher resolutions, reductions in cost, and increases in speed. 3D-printing systems can now create objects out of a wide variety of materials, including paper, plastic, ceramic, and metal. As 3D- printing technology advances, it will be able to handle even more exotic materials. For example, medical implants may be created with drug molecules built-in to be gradually released into the body. Nanomaterials like graphene could be used to create lightweight bulletproof clothing and superfast electronics. 3D printing can also benefit from advances in artificial intelligence, such as software that can optimize an object’s strength, aerodynamic shape, or other properties, and even create designs requiring shapes that would be impossible to manufacture with contemporary methods.
New, intuitive software is making it easier for people to create 3D-printed parts without advanced training. As 3D printing has become more widespread, it has begun to revolutionise the manufacturing industry. One major advantage is that it enables inexpensive and fast prototyping. Engineers can design a new part on a computer and hold a 3D-printed model in their hands within minutes or hours – a process that might have taken weeks with previous technology. This allows for rapid cycles of testing and modification for a fraction of the cost of old methods. As a result, people with good ideas but relatively little money can bring their innovations to the marketplace and benefit society.
Another key advantage of 3D printing is that it permits levels of customization that are not practical with mould-based manufacturing. Even a slight modification usually requires an entirely new mould, which can cost tens of thousands of dollars or more. By contrast, even major changes to a 3D- 3D-printing design carry no additional cost. As a result, inventors can have exactly the right parts they need to innovate, and consumers can affordably access products designed especially for them. One example among many is producing shoes made to the exact measurements of a customer’s feet for greatly enhanced fit and comfort. A leading 3D-printed footwear company is FitMyFoot, which lets customers use an app to take photos of their feet that are automatically converted into measurements for the printing process. Similarly, furniture can be moulded to fit every body type, and tools can be made to precisely fit your own hand. Of even greater importance, vital medical implants will be cheaper and more effective.
In addition, 3D printing allows manufacturing to be decentralised, empowering consumers and local communities. This contrasts with the paradigm that developed during the twentieth century, in which manufacturing is largely concentrated in giant corporate factories in major cities. Under this model, small towns and developing countries must buy their products from far away, and shipping is expensive and time-consuming. Decentralised manufacturing will also have significant environmental benefits. Shipping products from factories to consumers hundreds or thousands of miles away generates enormous emissions. According to the International Transport Forum, freight shipping accounts for around 30 per cent of all carbon emissions from fuel burning. Decentralised 3D printing can make much of that unnecessary.
Each year the resolution of 3D printing is improving and the technology is getting cheaper. As resolution improves (that is, the size of the smallest attainable design features shrinks) and costs fall, the range of goods that can be economically printed will grow. For example, many common fabrics have fibres with diameters that are 10 to 22 microns (millionths of a meter) wide. Some 3D printers can already achieve a resolution of 1 micron or less. Once the technology can achieve fabric-like diameters with fabric-like materials at similar prices to regular fabric, it will be economically feasible to print out any clothing we wish.271 Because printing speed is also increasing, high-volume manufacturing will become more practical.
In addition to manufacturing everyday goods like shoes and tools, new research is applying 3D printing to biology. Scientists are currently testing techniques that will make possible the printing of human body tissues and, ultimately, whole organs. The general principle involves a biologically inactive material, such as synthetic polymer or ceramic, printed into a three-dimensional “scaffold” in the shape of the desired body structure. Fluid rich with reprogrammed stem cells is then deposited over the scaffold, where the cells multiply and fill in the appropriate shape, thereby creating a replacement organ with the patient’s own DNA. United Therapeutics (a company for which I am a board member) is applying this approach (and others) to someday grow entire lungs, kidneys, and hearts. This method will ultimately be far superior to transplanting organs from one person to another, which has profound limitations in terms of availability and incompatibility with a patient’s immune system.
One potential drawback of 3D printing is that it could be used to manufacture pirated designs. Why pay $200 for a pair of designer shoes if you can download the file and print them for yourself at a fraction of the cost? We are already facing similar issues with the intellectual property of music, books, movies, and other creative forms. All of this requires new approaches to protect intellectual property.
Another troubling implication is that decentralized manufacturing will allow civilians to create weapons that they otherwise couldn’t easily access. Files are already circulating on the internet that enable people to print the parts to assemble their own guns. This will present a challenge for gun control and allow the creation of firearms with no serial numbers, making it more difficult for law enforcement to trace crimes. 3D-printed guns made from advanced plastics could even be used to bypass metal detectors. This will require a thoughtful re-evaluation of current regulations and policies.
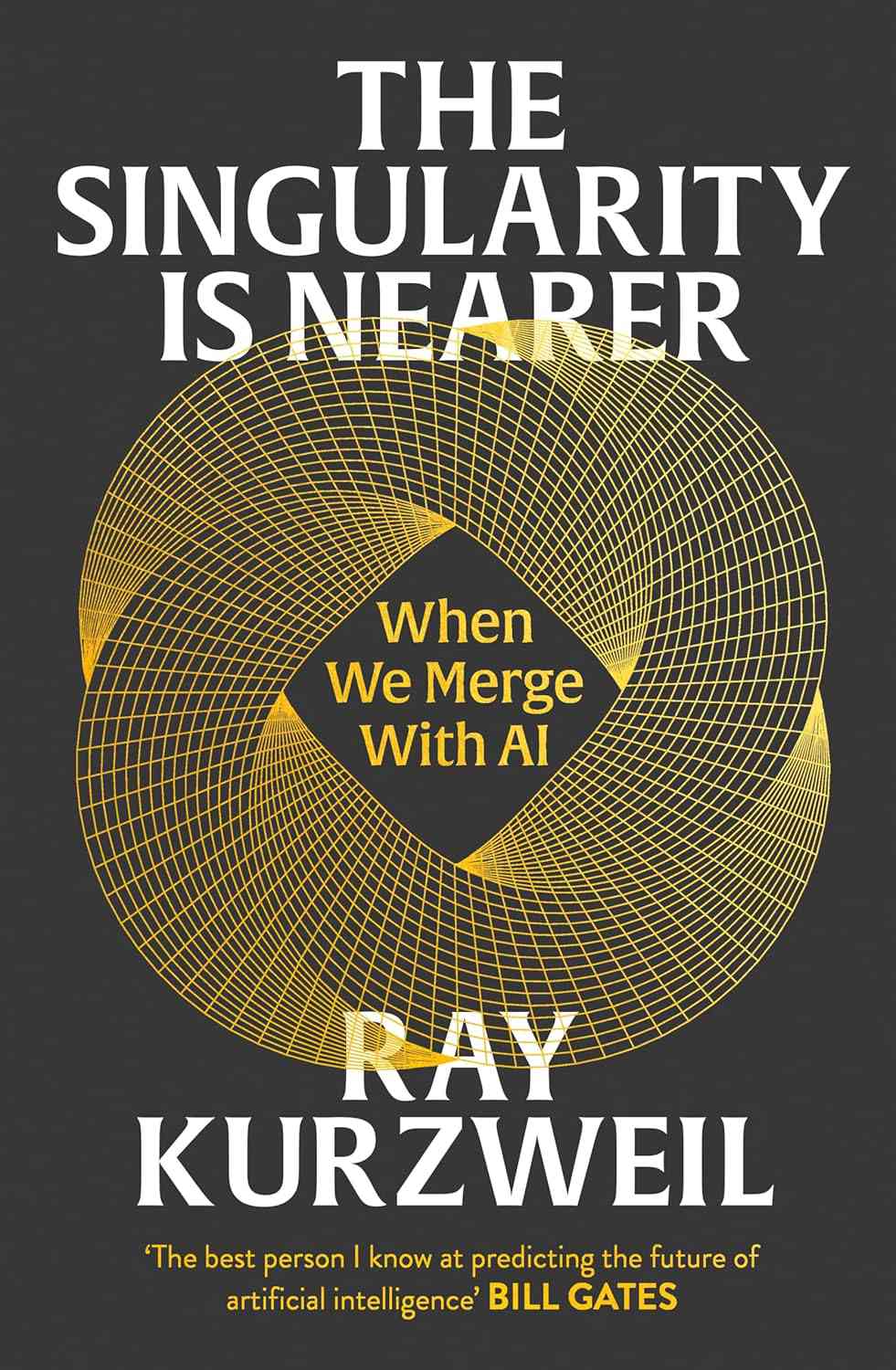
Excerpted with permission from The Singularity is Nearer: When We Merge with AI, Ray Kurzweil, The Bodley Head.