In Assam’s Baghjan area, an oil well that caught fire nearly three months ago is still burning. After several futile efforts to plug the leak, Oil India Limited has decided to try a different tack. It plans to “partially produce” natural gas from the well once again.
“A large amount of the gas coming out will directly be hooked on to a reproduction set-up near the well, and the rest of the gas will be flared,” said Tridiv Hazarika, the company’s spokesperson. “If we are successful, it will provide immediate relief to the local people as the fire and sound will disappear.”
Well number five at Baghjan had a blowout on May 27, when it started to leak natural gas and condensate uncontrollably. On June 9, the well caught fire. The blaze soon spread to the neighbouring area, an eco-sensitive zone replete with wetlands and tropical forests, burning down houses, fields and farms on its way, and killing two firefighters.
Months later, the well continues to expel fire accompanied by the loud humming noise of leaking gas. Thousands of people from neighbouring villages continue to live in relief camps.
Hopes of plugging the leakage appear to be increasingly bleak, admit Oil India Limited officials. All traditional methods have failed and there are fears about whether the well’s structure will hold. Hence, the unusual solution of starting partial production again.
‘Last resort’
Hazarika admitted the plan was “innovative”, though “technologically possible”. But independent experts took a grim view: starting production again was the “last resort” in the “worst-case situation” in a blowout.
“They will have to drill a substitute well nearby and divert the gas to it,” said a serving senior drilling engineer at Oil and Natural Gas Corporation of India with 35 years of experience. “It is possible, but there are lots of ifs and buts.”
Sumit D Malik, an independent drilling consultant with more than 15 years of experience in oil and gas majors like Cairns India and Schlumberger, largely agreed. “It can be done provided they have taken care of all the precautions and well integrity is maintained at all times,” he said.
Malik said that if the plan works, it will “certainly reduce the impact on the environment”. “The problem of fire will be solved to a certain extent but not entirely as they still have to flare some of the gas,” he said.
Ditto for sound, said Malik. “Sound will not disappear completely, but it will reduce as when you are diverting some of the gas, you will also divert some of the pressure,” he said.
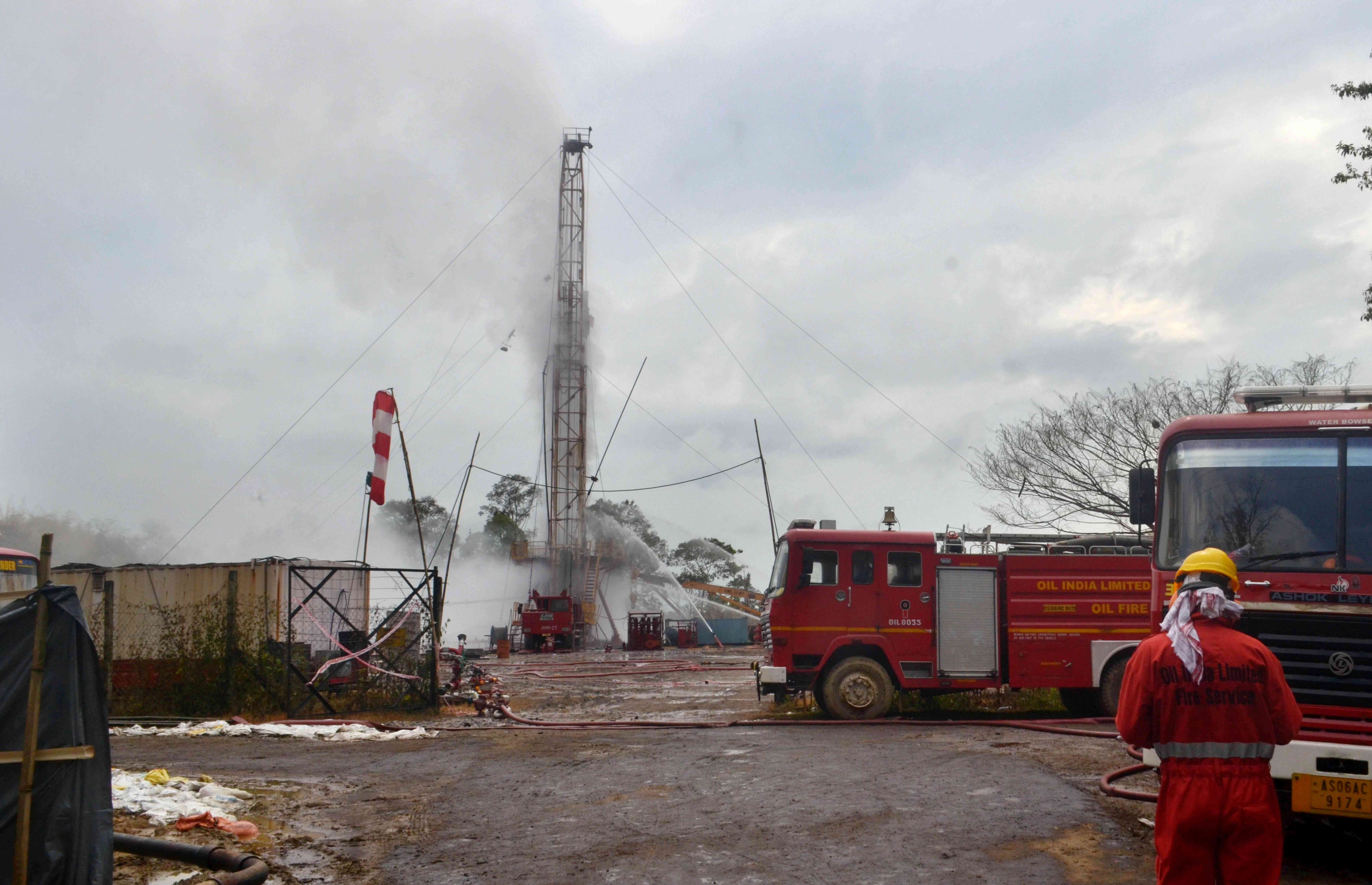
Pandemic, flood and fire
But how did things come to such a pass that Oil India has been forced to fall back on a method that can only partly fix the problem? Why did the conventional blowout control methods fail?
Oil India’s attempts to plug the well have been plagued by setbacks from the start. First, it was the Covid-19 pandemic that delayed the arrival of foreign experts. Soon after they arrived, a bout of torrential rains meant that the area was water-logged and all work had to be suspended.
In July, operations were already running well behind schedule – the company had initially estimated that it would take about a month to plug the well. That was when three of the foreign experts suffered burn injuries in another mini explosion, which spread the fire laterally.
The case of the blowout preventer
Earlier this month, there was finally some good news as the company finally managed to mount a blowout preventer on the mouth of the well. A blowout preventer is a large valve that is mounted on the surface on top of a gas or oil well. It keeps a tab on the pressure of the gas and caps the flow of oil or gas in case of emergencies. Simply put, it is equipment to prevent blowouts.
But since a blowout had already occurred in this case, the well also had to be killed for the leak to be plugged. To do this, extraneous pressure greater than the pressure at the production sand – the underground zone from which natural gas is extracted – had to be applied. This was to be done by pumping in mud through the blowout preventer. In an ideal situation, the mud would enter the perforated sand, block the pores, and stop the gas from gushing out after a certain point.
The killing operation, the company had predicted, would be completed within 24 hours.
But things did not go to plan. After some 88 barrels of chemical mud had been pumped in, a socket connecting the casing pipes that bring the gas up to the surface gave way. This resulted in the mud leaking into the space between the pipes. Pumping was immediately stopped. “It could not withstand the pressure as it was exposed to heat for the last two months,” said Hazarika. “We had anticipated this challenge, but we took a risk as we believed it could withstand around half an hour of pumping.”
Attempts to repair the damage also failed. “Finally, a decision has been taken that it would not be feasible to kill the well as we had planned as the integrity of the well had become questionable,” said Hazarika.
However, the company has not entirely abandoned its efforts to plug the leaking well. It now plans to import a “snubbing unit” and manpower to operate from it most likely from Canada – the technology is not available in India. A snubbing unit, Oil India officials said, attacks the target sand – the gas production zone – directly and does not involve any physical interaction with other surfaces of the well. “This would do away with surface level challenges,” said Hazarika. “This machine is used when you are absolutely convinced that traditional killing cannot be done because of surface level weakness and integrity questions of the well.”